
To lay out the teeth on a non-circular gear one would simply determine the pitch circle for each tooth on the gear and proceed normally using Unwin's Construction as if that tooth were on a circular gear. A method called Unwin's Construction was commonly used and is still used internally by CAD programs to calculate involute tooth shape. Back when everything was done by draughtsmen on paper a it was normal practise to actually draw the teeth accurately to scale. Prior to the use of involute gearing there were pretty good compromises that were a lot easier to lay out.Įven if involute teeth are used laying it out isn't difficult, just tedious. There is no particular reason they must be made with involute teeth.
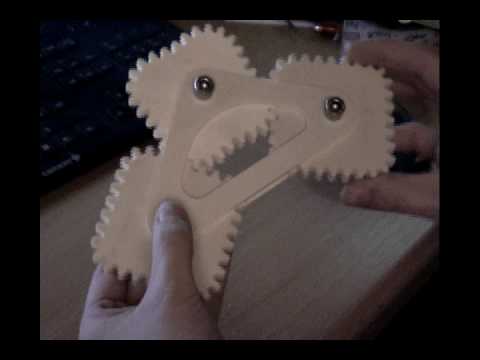
At least I think it would.Īnybody know how such gears are actually cut?
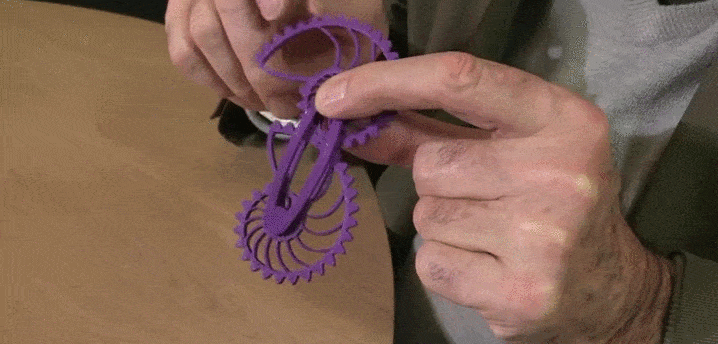
This would tend to generate teeth that would mesh with a rack that also moved in relation to the gear in the same manner. The best idea I can think of is to use a hob and while the blank rotates, it also moves back and forth toward and away from the hob. Would two ellipses rotate together in contact with fixed centers? If not, what curves would do so? Ovals? The question is complicated by the fact that the poing of contact between two such curves may not necessairly be on the line between their centers at all points in the rotation.
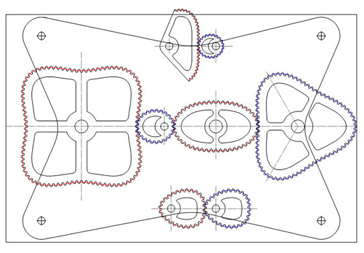
I am not even sure that the shape of the pitch line is even an ellipse. Probably even the two flanks of a single tooth (or space) are different. What I wonder is how are such gears cut? I would think that each tooth is a different shape from the ones next to it. I saw an ad in the latest HSM with a drawing of such a pair of gears and it brought back the fascination. The driver was turning at a constant speed and the driven gear would cycle from faster to slower twice each revolution. They were the same tooth count and were meshed with the high spots on one matched to the low spots on the other.
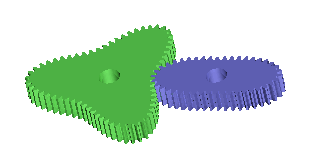
The pair that I was most fascinated by was two that were cut on blanks that were probably elipses instead of circles. They were all meshed together and a motor drove the exhibit to demonstrate the actions of the various types. It contained almost every type of gear from simple spurs on up. Years ago I observed an exhibit in a showcase that was placed in the main lobby of the New Orleans International Airport by a local shop that made gears.
